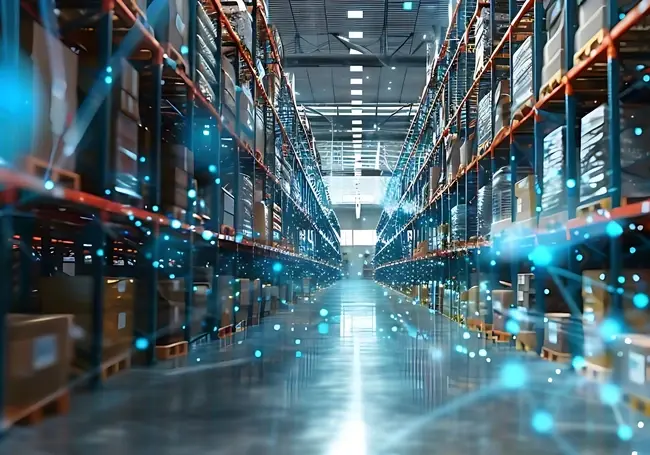
No business wants to see customers walk away due to stock outages. But especially in difficult market conditions, few companies can afford to have excessive working capital in costly overstock. This is where inventory optimisation comes in: the process of attempting to position stock levels to meet customer demand, while minimizing inventory-related expenses.
A new generation of advanced analytics and supply chain management technologies are transforming the ability of companies to make more accurate forecasts, and respond with agility to changes in demand and availability. Here’s a closer look at what the modern approach to inventory optimisation involves, and how to put your strategy into practice…
What is Inventory Optimisation?
For producers and retailers, inventory optimisation is the technique of maintaining “just the right amount” of stock; i.e. enough to meet the current and upcoming demand of customers, while minimising the financial costs, opportunity costs, and operational risks that come with holding too much stock.
Inventory Optimisation vs Inventory Management: Is There a Difference?
Inventory management covers all of the practices and processes involved in ordering, controlling, tracking, and utilising inventory.
Inventory optimisation forms part of this wider inventory management framework. It refers specifically to the process of achieving the right inventory balance between supply and demand at minimal cost to the business. Getting it right requires comprehensive analysis of all of the factors that influence actual and required inventory levels, costs, and service efficiency. The areas you need to analyse include the following:
Demand analysis. Assessing historical demand patterns (e.g. seasonal trends and recent sales patterns). Factoring in external factors, such as broad market trends, economic conditions, and activities of competitors. Using statistical forecasting and demand sensing to pick up on sudden and unexpected demand shifts.
Lead time analysis and supplier performance. Using supplier performance monitoring and lead time tracking systems to determine the time required to replenish inventory, and to evaluate how supplier reliability impacts inventory needs.
Stock classifications. Using ABC analysis - i.e. categorising items based on their importance - to prioritise inventory based on value and volume. Calculating buffer stock requirements and identifying optimal stock levels of different items.
Cost analysis. Calculating holding costs (storage, insurance, and depreciation), costs associated with procurement and replenishment to find ways to minimise total inventory costs.
What Is Multi-Echelon Inventory Optimisation?
Effective inventory optimisation requires you to look way beyond the walls of your business. A 2024 McKinsey survey suggested that nine in ten businesses had experienced supply chain disruption over the last 12 months. All it takes is a single incident involving one of the links across your supply chain - e.g. a production facility going offline, a container getting stranded, or a sudden price hike from a particular supplier - and it can completely skew your assumptions and calculations.
Multi-echelon inventory optimisation (MEIO) reflects this reality. Rather than focusing solely on your business, and on assessing the performance of individual suppliers in isolation, it seeks to optimise inventory levels across multiple stages (i.e. “echelons”) of that chain. The aim is to increase your supply chain’s resilience in the face of outages or demand fluctuations, while also helping you avoid excess holding costs, transportation costs, and stockouts.
Here’s how MEIO works:
Data collection. For each echelon, you gather data related to demand (historical and forecasted), typical lead times between echelons (e.g. the time it takes from goods to reach your regional warehouses from the manufacturer’s central distribution centre), as well as data on holding, ordering, and transportation costs.
Modelling. You build a mathematical model of the entire supply chain, including the relationships between all echelons.
Inventory optimisation calculation. A combination of linear programming, simulation, and machine learning algorithms are deployed to calculate optimal inventory levels at each echelon, replenishment policies and frequencies, and placement of safety stock (to account for unplanned outages/events).
Building an inventory optimisation strategy: what capabilities do you need?
Centralization and Data Integration
According to Deloitte, only 13% of businesses can map their entire supply network. If you cannot see what is happening at each stage or echelon of your chain, it becomes impossible to make the right decisions on what levels of inventory you need, and where.
Inventory optimisation requires you to analyse data from multiple areas of the business (e.g. sales, fulfillment, finance, and procurement), as well as from third parties (e.g. suppliers and logistics partners). As a starting point, you need a joined-up view of all of this, so data centralisation and integration should be a foundational priority. Pay special attention to cloud-based enterprise resource planning (ERP) systems (SAP and Oracle, for instance), which give you the ability to aggregate and harmonise data from all areas of your business, including your wider supply chain.
Real-Time Inventory Tracking
With the ability to track inventory as it moves from stage to stage through the supply chain, you are much better equipped to identify the exact location of items, and identify any bottlenecks within the chain. IoT (Internet of Things) enabled sensors and RFID tags enables stock movement to be tracked at a granular level.
Integrating it into a real-time dashboard within your ERP system means you can put this data to work; using it to check that inventory is where it is meant to be across the chain, liaising with suppliers where needed to address any holdups, and making better-informed replenishment and reordering decisions.
Demand forecasting
When is your next sales spike or downturn likely to arise? Which specific product segments are likely to be affected?
Self-service business intelligence tools (e.g. Power BI and Tableau) can equip you to understand historical performance on both the demand and the supply side. To go beyond this, and to enable decision-making based on forecasted future trends and demands, look for predictive analytics capabilities (examples of solutions that deliver this include Anaplan, SAP Integrated Business Planning for Supply Chain, and CCH Tagetik Supply Chain Planning).
What next? Bringing the elements of inventory optimisation together
Can our decision-makers access accurate and up-to-date inventory data?
How accurately do we forecast demand?
Are our current safety stock levels sufficient to avoid stockouts? But at the same time, are we holding excessive stock in certain categories, leading to high carrying costs?
Is our replenishment strategy optimised for our particular supply chain?
Is there a link between particular suppliers and stockouts and/or high inventory costs?
Inventory optimisation is not a once-and-for-all exercise. Rather, it involves constantly asking the above types of questions. If your current capabilities prevent you from answering them with confidence, it’s a sign that this area is a prime candidate for digital transformation within your business.
Comments ( 0 )