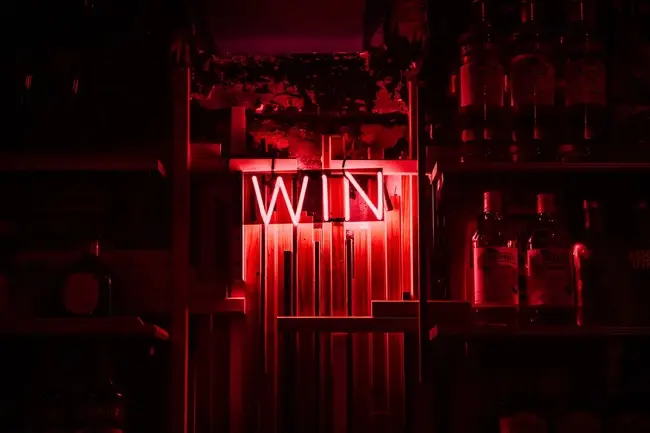
Ask most warehouse managers what they want to achieve in 2023 and a large proportion will say ‘rapidly improve business efficiency’ and ‘cut opex overheads’. They might also answer, ‘find a way to prevent mistakes’, or ‘reduce our reliance on temp workers’ or simply say ‘avoid bottlenecks in the warehouse’. Ask about whether they are using technology to support their warehouse operations and many of the professionals facing these problems will probably say no, and admit to relying on a paper-based warehouse system. That’s why they are having these issues.
The biggest single factor influencing how efficiently a warehouse can run is whether or not it is technology driven. If you want a streamlined, successful warehouse operation to improve your bottom line, this journey starts with the introduction of a dedicated warehouse management system (WMS). A WMS can track the flow of all goods, from arrival at the warehouse, onto packing and dispatch, before tracking the final order journey to the customer’s delivery address.
Considering this point a different way, if all your competitors are adopting new technologies and benefiting from the advantages brought by a WMS, your reliance on paper-based systems will make it ever more difficult to compete.
Paper-based warehouse management systems have long outlived their usefulness for many companies. Even smaller warehouses can take advantage of the tools and data that are part of a WMS system and new ‘light touch’ software solutions are available to make the transition as fast and low cost as possible. Here are a few of the ways a WMS can remove the common bottlenecks from paper-based warehousing that may be holding you back.
5 of the warehouse bottlenecks removed with a WMS
Goods receiving and put away
Stock comes into the warehouse all the time, whether it is raw materials for manufacturers, or finished goods to be sold on. This is the lifeblood of the business but it is only working for you if it is available either to be sold, or made into something that can be sold. Whilst it is sitting in the warehouse waiting to be booked in, this stock is just an overhead, it is costing money (and maybe also creating an obstacle to get around).
A WMS will help to automate booking stock in, making it immediately available on the system either for selling, or for use within production. It also helps find locations for stock items and this can mean up to 30% more stock gets properly stored in easily identifiable locations, in a given area of space.
Using a WMS, the whole operation can be project managed efficiently by the software to bring the minimum level of disruption.
Order picking
This is the classic area people first think of when considering a WMS and it is the function where huge process efficiency gains can be seen instantly. Picking is one of the activities in every warehouse that can make or break the efficiency of your whole logistics operation. Switching from paper to a WMS means orders can be picked and sent out to customers as quickly and accurately as possible. It also allows companies to shorten their order cycle times, with shorter lead times to help create a competitive edge and faster payment cycles. This is especially important for e-commerce businesses where fast, inexpensive delivery is a key purchase driver.
Using a WMS you can choose how to pick, whether you are focusing on bulk orders or single items to be picked as part of a ‘wave’. Or perhaps a combination of the two, depending on the time of day. Your business is likely to have its own unique needs and a WMS can support you with additional functionality that would normally take up time to record accurately on a paper-based system. You might need item level traceability and shelf life rotation, or need to cater for a very high throughput of products. Whatever your requirements, a WMS will work in real-time - as soon as items are picked, stock levels are automatically adjusted. If you were running on paper, this data would need inputting after the event, causing delays and bottlenecks.
Voice picking is one of the fastest growing methods used to improve order picking productivity and a WMS supports this way of working. By allowing your picker to carry out two-way communication with a WMS, they will be able to operate hands free. It is particularly useful in cold chain cold storage environments where pickers might be wearing protective gloves or where the warehouse stocks very high numbers of small items. Imagine having to work with paper pick sheets when you could be flying through the day’s orders, guided by technology.
Packing bench
In an efficient warehouse, goods travel to and from the packing bench quickly and with as much automation built into processes as possible. Using a WMS, it is possible to scan the entire contents of a box in one go and have an instant audit trail created, without the need to individually scan items. The system knows what is in the box and where each item ultimately needs to go, whether that is in a single consignment or split into multiple orders. Once items are checked out, the system can also spot opportunities to reduce the numbers of consignments sent to parcel delivery firms, saving on transport costs and packaging. A WMS also offers a high degree of process flexibility, with the chance to choose whether a single order is picked and packed by the same operative or picked and sent to a packing team who can then check for accuracy. It is a choice between having accountability for orders lying with one individual or building quality into the process with independent verification. Both are easy to roll out and errors will rapidly become a distant memory.
Stock counting
Shrinkage can be a real problem in warehouses and completing a regular stock count is part of ongoing warehouse management. The problem with stock counts is the time they take. Counting is effectively dead time that could be better spent elsewhere. Using a WMS, it is possible to interweave transactions like stock counting with picking. When operatives are gathering the items for an order, they can do a stock count as they go about their pick walk, saving time and also ensuring that stock figures are always right up to date.
Counting as you go, also known as perpetual inventory management, has another very important benefit, it also ensures that stock discrepancies are found far quicker than would be the case in a four walls count and reduces the need for “distress” counting when a particular item issue has been found. The WMS takes care of everything, by tracking likely stock requirements based on historical ordering patterns and automating the replenishment reminders. It is extremely difficult (and time consuming) to manage ongoing stock counting and replenishments as efficiently as this using only a paper-based system.
Returns management
Every e-commerce company’s biggest headache, returns are notoriously time consuming to process. It is like doing goods receiving all over again, but this time the items need to be quality checked too. Just like before, these incoming stock items are not working for your business until they are booked in and with a WMS this is as immediate as it can possibly be. When the WMS is integrated with an e-commerce store front, goods can even be put back up for sale the second they are checked back in as part of a returns management process. You could never achieve that level of efficiency with a paper-based system.
Many businesses have made the transition from managing their warehouses using paper to full blown automation with a WMS. There are countless examples showing how businesses in diverse industries, from fine ales to furniture, dog collars to designer underwear, whisky to walking boots are seeing a rapid return on investment. Imagine a warehouse without paper, how much better would it be?
Comments ( 0 )