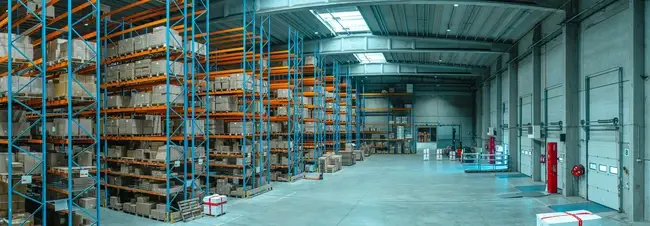
When the topic of warehouse metrics comes up in discussions with customers, the one that’s most frequently quoted as being the de facto performance yardstick is OTIF, ‘on time in full’. Our experience has shown that although OTIF is a useful measure, there are others that are equally, if not more important. This is because OTIF is an umbrella metric and underneath it lay many other sub-activities that will impact whether or not an acceptable rate can be achieved in your warehouse, as this article highlights.
Using a WMS (warehouse management software) system makes it easy to capture all the rich data that’s constantly being generated in the warehouse and transform it into commercial information. Information that can be used strategically, to improve business performance and profit margins. Over time, by measuring the right metrics, your business will also offer a better, faster service to customers and develop the reputation you have always wanted to achieve. Here are some of the most valuable metrics you can get from your WMS.
Average Stock to Dock time (ASD)
Average Stock to Dock is a very useful measurement that indicates how well stock is moving through the warehouse. It records how long it takes for stock items to arrive in the warehouse and then either be picked for an order, or moved about during cross docking process. ASDT tells management when the items arrived on the loading bay and the point in time when the stock was available to the system (booked in) to be picked for an order or for cross docking. Dock to stock times are really important because there's no point having a system that allows stock to arrive in the warehouse and experience a delay before it is available for sales orders. This is especially important for e-commerce businesses - the faster the booking in time the better and this is a metric that conveys that rate to warehouse managers.
Average Order to Dispatch Process time
Average Order to Dispatch Process (AODP) indicates the length of time that elapses between when an order is placed to the item(s) actually leaving the warehouse for the customer. Apart from improving efficiency levels and keeping customers happy, this metric is extremely important for warehouses with perishable items and it needs to be as low (in time) as possible.
Audit to Dispatch Process
Linked to Average Order to Dispatch measures is the Audit to Dispatch Process metric. This is relevant for warehouses employing stock rotation, date control and batch number monitoring. For instance, what process is followed when items first arrive into the warehouse if goods with a shorter expiry date are already available for shipping. Ideally you will be retaining the newer consignment and shipping out the older stocks if you are rotating stock levels properly.
The Audit to Dispatch Process also monitors when an order was placed plus when and where the items were released. For instance, was the stock released from the credit held capability? When was the stock allocated onto the system? When was it released into the warehouse picking pool? When did people start picking it? And when did they finish picking it? When was it dispatched? When was it labelled for courier collection. These time sensitive metrics are very significant for improving efficiency levels.
One reason why insights like these are so important is because they provide an understanding of how well operatives are prioritising workloads. Many warehouses I have visited have operatives busy picking orders that are not due for dispatch on the same day. At the same time, other more urgent orders are piling up on the packing bench and need to be shipped out to customers.
Overall audit to dispatch time also indicates how many open orders there are at any one time, how many orders or tasks are outstanding for the day and very importantly, whether there are orders overdue. By referring to the average pick time metric, it’s possible to precisely calculate how long it would take to clear the audit pool and whether more resource is needed. It is a really key metric.
Warehouse occupancy levels
Another important metric given both the cost of warehousing space today and the intermittent supply disruption many businesses are facing is warehouse occupancy. This is an important metric because it highlights how much storage space is available and whether it would be possible to store excess inventory if needed. For instance, there may be 10,000 available locations in the warehouse and only 83% of them are fully utilised.
Perpetual inventory/inventory accuracy reporting
Inventory accuracy is a huge topic and worthy of a blog in its own right but we will touch on it here. Shrinkage is an ongoing problem in many warehouses and how closely the actual inventory numbers tally with what the business thinks it has in stock at any time is a very critical metric. Having an accurate inventory management process will avoid a lot of time spent on distressed counting and it eliminates the need for four walls counts.
Implementing perpetual inventory management is one of the best ways to achieve this and in addition to minimising shrinkage, it also means replenishment processes can be synchronised with the picking cycle. There is no point having 50 pickers working on orders if every time they go to a location they have to stop and wait for the stock to be replenished for their order pick. It’s a very common issue in warehouses and can account for a lot of time wasted by operatives.
By highlighting these different metrics, it becomes clear why OTIF cannot be the only measure to use when looking at the performance of a warehouse operation. It’s basically an umbrella term and it’s impossible to achieve a good OTIF rate if the underlying processes aren’t as efficient as they could be. Using a best-of-breed warehouse management system, it becomes easy to drill down and separate the raw data from real information that can influence business performance.
Comments ( 0 )